The five main characteristics of a food pump
Maintaining high sanitary standards has become the top priority within the food and beverage manufacturing sectors. Compliance with hygienic processing and hygienic conditions aims to minimize all contamination risks that could damage the entire production process. Any damage from contamination of the final product or semi-finished products that contribute to the production process can cause three types of problems:
- production process inefficiencies: any product contamination can cause downtime that negatively affects efficiency and productivity.
- environmental and safety issues: contamination of a product can cause environmental or health issues for workers employed in the production process.
- economic losses: inefficiencies on the production side, damage to the environment or to workers lead to increased costs and significant revenue losses.
To maintain a high level of prevention supervision, it is necessary for food and beverage industry operators to employ equipment that is appropriate and in line with the regulatory requirements of the industry.
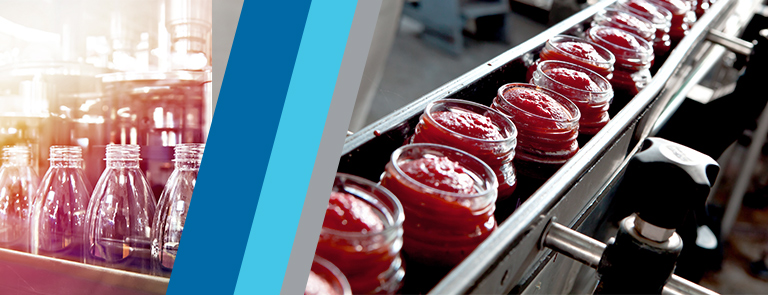
The new challenges for food pumps
In this context, double diaphragm pumps are among the most important equipment within food production processes. Food pumps must be able to efficiently meet the following needs:
- handle loading, unloading and transfer operations of a wide type of liquids characterized by low or high viscosity.
- operate within environments characterized by wide temperature ranges.
- to manage in a cyclic manner the cleaning and sanitization processes designed to prevent contamination.
Choosing an appropriate pumping technology requires careful consideration. Although there are several types of pumps on the market, we believe that double diaphragm pumps are the ideal solution for handling and transferring fluids within the food and beverage sectors. However, it is necessary for food pumps to meet certain requirements to ensure proper operation of the entire production process.
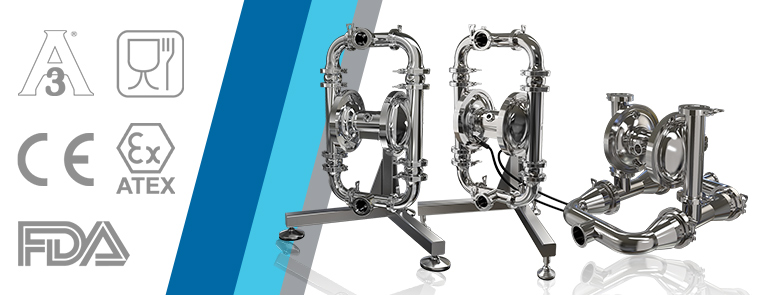
The basic characteristics of a food pump
Within this article, we list the five basic characteristics that a food pump must possess to ensure adequate conditions of efficiency and safety within the food production process.
1. Compliance with FDA, MOCA, 3A food regulations
Compliance with requirements under FDA, MOCA or 3A regulatory standards implies the use of materials suitable for contact with food and beverages. In this case, materials such as mechanically polished AISI 316 L stainless steel or food grade PTFE, used by Debem, are the best solution to reduce contamination risks and at the same time ensure a good life cycle of the food pump.
2. Presence of leak detection systems
To avoid the risks of liquid spillage, it is necessary for food pumps to be equipped with an appropriate leak detection system. In this case, Debem double diaphragm pump models are equipped with special optical sensors that can detect any rupture of the membranes and automatically stop the operation of the pump.
3. Ability to handle fluids with the presence of solid elements
Within food processing, it is very common to come across the need to transfer or remove processing waste, which often has solid features, even large ones. In this case, it becomes essential to be equipped with a pump capable of conveying fluids with suspended solids. Debem food pumps can be equipped with special eccentric ball valves that allow the passage of bulky solids within the fluid. Debem’s wide selection of AODD food pump models also incorporates pumps with special clapet valves to handle fluids with suspended solids up to 45 mm in diameter.
4. Ease of maintenance management
To minimize maintenance and repair work, it is necessary for food pumps to be designed in a simple and efficient manner with mechanisms composed of a small number of components. To ensure the smooth operation of food production plants, Debem AODD pumps are equipped with a coaxial anti-stall exchanger, a special patented technology that can ensure optimal performance and low energy consumption even under the most critical conditions. The anti-stall exchanger is built with a negligible number of components ensuring ease and intuitiveness in maintenance and repair operations.
5. Suitability to support washing and sanitizing steps
Food membrane pumps must be able to provide the necessary cleaning and sanitizing operations required by industry production standards. For this reason, Debem AODD pumps are equipped with a special rapid emptying system that will allow the fluid inside the suction chambers to drain from the pump. The pump will thus be free of internal impurities and ready to be flushed and sanitized.
Debem's offering for the food and beverage industry
Debem, a leading manufacturer of pumping systems for the food, cosmetic, pharmaceutical and trichological industries is able to support industrial food processes while ensuring compliance with the strictest food regulations. For any informational or commercial needs, we invite you to contact our sales team who will be supportive in choosing the most suitable pumping technology for the specific needs of the application sector.